
关于采用工业4.0技术实现制造业数字化转型的紧迫性已不言而喻。可以肯定的是,这些技术中的许多解决方案为无数的先进生产场景提供了独立的可行性。
然而,工厂实施的任何新技术,只有在其对工厂生产线上的物料流动产生相对积极的影响时,才是有效的。它应该带来可衡量的改进,如质量、产能、整体设备效率(OEE)或所有这些传统指标。这种实实在在的改进是通往下一代生产的成功之旅的开始。
随着企业信息技术(IT)和运营技术(OT)系统的融合,制造商正在转向实现更多连接和具有高级分析功能的解决方案,以更好地实现这些关键绩效指标(KPI),行业领导者也在尝试人工智能。这有一个很好的理由:数据。
通过数字化成熟度适应不断变化的目标
对于"最后一英里"的优化,工业企业感到压力,需要理解工业流程产生的TB级数据,而仅靠人类专家的能力是不够的。半导体晶圆厂是这种技术挑战的极端例子,但任何高级生产环境也是如此,从生产边缘利用数据至关重要。
工厂建立足够的数据过滤、预处理、可视化和可追溯性来完成这项工作。只有这样,它才能在数字之旅上迈出下一步。第二步决定了上述对生产过程的改进有一个关键维度:适应性。为什么适应性对于制造技术来说是不可或缺的?
首先,随着工业产品(以及制造它们的机器)的材料和功能的进步,限制生产的参数也在变化。其次,由于创新、科学发现、文化转变和全球环境力量,旧产品不断迭代,新产品也不断被发明。衡量任何工业4.0技术集成价值的关键指标是其对不断发展的新生产或现有生产流程的整体贡献。然而,尽管工业转型的持续适应性至关重要,但仅仅完成制造业的更大使命是不够的。
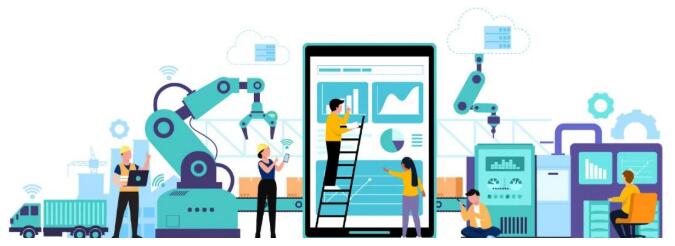
数据驱动的大规模创新
以数字为主导的扩展是更广泛的业务转变的一部分。从本质上讲,它以数据智能改变游戏规则的可能性为指导--已经在健康和金融等行业建立起来。例如,Gartner 的副总裁分析师Mike Rollings认为所有当代组织都必须进行运营转型,并坚称他们只能在数据运行显示的范围内实现它:
"首席数据官(CDO)需要与业务主管合作,以确定数据源、数据质量问题、分析类型和新的工作实践。很多时候,这导致人们意识到数据驱动的机会跨越了组织边界,需要改变运营模式才能实现预期的结果。"
在没有CDO的情况下,Rollings 仍然强调利用专门的数据专业知识成功"采用优先级或领导其数据和分析策略的任务"对组织转型的重要性。
新范式中需要的新指标
鉴于这些以数字为基础的巨变,让我们暂时想象一下智能制造的未来。它可能是一个泛运营、自我优化的生态系统。碳中和,并在循环经济的更广泛背景下发挥作用。
人类将需要被授权在未来提升他们的数字技能。随着制造专业人士与智能机器的交互,劳动力的数字技能重新校准将是必要的。负责质量、生产和维护的控制器、操作员和团队将参与关键的自动化任务、控制系统安装和迁移、远程系统监控以及其他不可预见的优化项目。
根据这一愿景,未来的制造业还将通过不同的指标来获取价值,例如社会和环境效益以及数字能力的可扩展性。根据 2022 年世界经济论坛白皮书《通过先进制造解锁商业模式创新》:
"公司需要利用其在先进制造领域的投资,不仅要优化运营模式,还要开启新的商业模式,为所有利益相关者创造和交付新价值,包括公司本身、工人、社会和环境。"
与所有伟大的工业变革一样,我们当前的时代超越了对孤立用例的持续改进。公司范围的调整必须超出离散生产事件甚至端到端操作的水平。对于制造商来说,这意味着对可用技术和与之交互的人有不同的思考。
工业4.0思维方式的转变
我们所处的工业时代以跨学科协作方式为前提。部门孤岛将被整合并嵌入到一个互连的网络中。因此,接受更大的制造使命需要采用和利用新技术的战略思维转变。这种变化与上述不断扩大的复杂性和工业的快速技术进步是相称的。在实践中,这种新的思维范式带来了两个转变:
· 它让制造业专业人士在OT和IT融合的前沿领域占据主导地位。
· 它使工业企业能够重新定义如何在不断变化的环境中灵活地获取价值。
实施全新的商业模式听起来像是一个雄心勃勃的理想。然而,正如世界经济论坛所建议的(以及制造灯塔所显示的),它已从生产层面开始。所以,正确的问题是:先进制造业如何成为更全面工业变革的风向标?
它始于一个完全连接的智能生产环境。有四个连接构件,它们必须为自适应IIoT平台奠定基础,以实现价值。
首先,在数据感知层,工厂可以确保传感器、机器、边缘设备(具有实时AI和计算能力)和数据库的灵活集成。感知层建立了一个基础,IIoT平台可以从中成功地联网、收集和存储其边缘数据。
数据的收集方式多种多样:通过可编程逻辑控制器(PLC)、监控和数据采集(SCADA)系统,以及制造执行系统/质量管理系统(MES/QMS)。至于数据存储,边缘到云的整合为不断发展的生产环境提供了安全、保障和远程访问。在网络层,专家可以确保通过众多协议进行无缝通信。
然而,一个连接解决方案在感知、网络和存储到位的情况下还不够完整。完全连接发生在上层应用程序。如果制造企业最重要的战略目标是充分嵌入技术创新以改变其运营模式,那么全工厂的连通性是必要的,但还不够。工业企业需要一种技术干预来准备大规模执行下一代生产。

图 1:良好的连接平台可实现集中、实时的报告和直观的分层数据可视化。本文图片来源:Dataprophet
AIaaS是如何工作的?
面对日益增加的IT/OT复杂性,内部资源限制(如员工流失和数字技能差距)变得更加明显。因此,必须注意的是,实现智能工厂目标不仅仅是将适当的IT和OT基础设施组合在一起。工厂经理和高管必须确保有足够的专业知识来管理这些技术,并以最佳方式执行新时代生产的数字化转型。
AI 即服务 (AIaaS)将支持AI的IIoT 平台与自动化深度学习智能相结合,以帮助加速实现更大的制造使命。它通过规范化灵活、敏捷和协作的制造,在生产层面实现这一目标。AIaaS是如何工作的?
它从AI准备情况评估(深入研究工厂的流程和质量数据系统)开始。这种探索产生了关于规范性AI成熟度的清晰报告。一旦建立了数字化成熟度,AI系统就可以被安装并从边缘到云再到网络。调试测试展示了AI系统的影响并量化了其价值。
在整个过程中,网络工程师、IT系统所有者、工厂运营人员、生产操作员和控制工程师与外部数据科学家和软件工程师进行互动。工厂团队首先根据商定的 KPI 基准,为特定生产线协作部署数据衍生的 AI 解决方案。这个过程通常需要3到4个月。
在完成安装和调试测试后,AIaaS 提供商确保持续访问、报告、培训、支持、完整的模型维护和自适应改造 AI 系统。
ROI 保障的制造智能自动化
理想情况下,面向制造的AI部署是一种运营支出(OpEx)解决方案,它通过从工厂已经拥有的数据中提取可衡量的投资回报率来获得其价值。对于制造环境而言,最具影响力的AI是作为规范性分析应用的深度学习。
它解析来自学习的生产多方面的实时和历史数据,以发现最佳操作制度。这些都是作为工厂运营商的优先处方提供的,以制定积极的设定点调整,以便在生产损失之前获得最佳的生产结果。一切都在不阻止生产或将其置于危险之中的情况下实现。
善于利用深度学习的制造商可以不断推动即时和可衡量的流程和机器健康状况的改善。他们之所以能够做到这一点,是因为最好的 AI 部署创建了一个生产反馈循环,系统通过流程的每次迭代来学习--自动进行根本原因分析并嵌入专家执行,这成为系统动态、不断增长的智能的一部分。

图2:利用深度学习处方的制造商可以不断推动即时和可衡量的过程和机器健康的改善。
围绕可扩展的 AI 协调团队
这些 AIaaS 部署还协调了以前孤立的团队。生产、质量、维护、工厂操作员和工艺工程师每天都可以与集中式、自洽的系统进行交互。
此外,还内置了可扩展性。深度学习本质上与制造过程无关,其内核是高质量的工业数据。因此,一旦它在一条生产线或一件制造设备上证明了其有效性,就可以将其推广到其他重复或类似的生产线。企业还可以将其应用于新产品和产品变体,从而为快速提升至关重要的新建运营提供面向未来的人工智能驱动生产。
扩展深度学习创新
为了利用这种规模化、端到端的生产数字化转型所捕获的价值,下一级创新必须扩展到整个价值链。端到端扩展AI实施可以进一步降低运营成本,从而提高整个价值链的利润率。此外,它可以通过正确的战略部署不断地做到这一点。
通过在工业现场级别进行基于AI的数据分层和 AI 驱动的优化,数据驱动的价值推动因素在其他地方更容易实现。这些推动因素包括产品需求预测和动态生产计划。经验丰富的数据科学家可以使用前面提到的自我优化自治循环,调整AI的自动化智能,以便在供应链波动的情况下完成订单。
至于采用新的指标来衡量成功,深度学习作为规范性分析应用是一种合适的技术。捕获数据并维持自主反馈循环建立了一个工作模型,用于以不同的方式感知生产问题(以及扩展的运营问题)。
例如,可持续性与任何传统的生产目标相差不远--更高效地运行,减少废料或延长生产线的使用寿命等。深度学习擅长识别生产制度中的固有偏见。在这种情况下,AIaaS提供商可以与工厂人员合作,找到一种方法,可以在不影响质量或吞吐量的情况下最大限度地提高OEE测量的准确性。
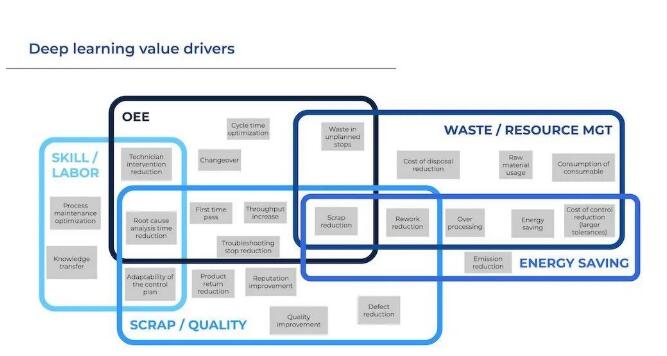
图 3:深度学习擅长识别生产制度中的固有偏差,并且可以在不影响质量或吞吐量的情况下最大限度地提高准确的OEE测量。
AIaaS推动了数字能力并促成了全系统范围的协作。制造商需要重塑他们在不断变化的环境中定义和获取价值的方式。数字创新的影响需要在每个阶段进行衡量。建立数字化成熟度并维持 AIaaS 执行的智能系统可确保持续的投资回报率。除此之外,它还使先进的制造商能够追求其更广泛的目标,并通过调整商业、社会、环境和客户基准并在业务发展过程中获取滚动价值来量化目标。
一旦在生产环境中得到验证,随着工业企业巩固其战术实施中积累的专业知识,人工智能的应用将变得更加具有战略性。为了使AI成为力量倍增器,制造商必须扩展用例并将其扩展到组织的其他领域,并衡量整个价值链的可行性和影响的最佳点。
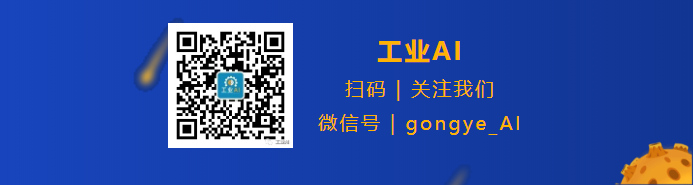