
还记得小时候玩的变形金刚吗?今天我们要聊的机床,可是工业界真正的"变形金刚"!作为制造业的顶梁柱,它正在经历一场前所未有的进化。智能时代来临,这位"工业巨星"也要跟上潮流——不只是要跑得快、做得准,还要更聪明、更智能。就像升级打怪一样,机床不断突破自我,解锁新技能:自动化、智能化……。制造商们摩拳擦掌,用新的传动技术和控制系统,让机床华丽变身,只为在工业4.0的竞技场上赢得主角地位。这场工业革命的大戏,才刚刚开始精彩!

机床行业代表性设备之一的双端面磨床,作为一种高效的平面磨削设备,广泛应用于各种高精度工件的加工中。它通过特别的结构和先进的技术,实现了对工件上下两个端面的精准研磨,确保了工件的高平面度、平行度和表面粗糙度。现代双端面磨床普遍采用数控(CNC)系统,能够精确控制加工参数,如磨削速度、磨盘压力、进给量等。
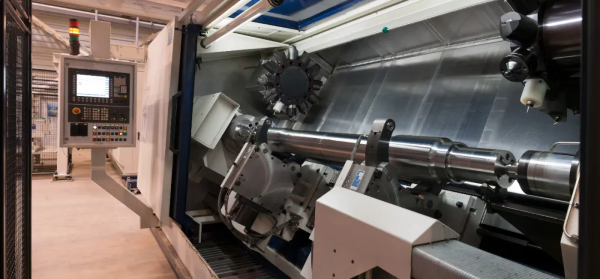

随着工业自动化和智能制造的推进,加工标准和市场竞争日益严苛。一方面,双端面磨床需要实现更高的动态特性和控制精度,更高的进给速度和加速度;另一方面,提升加工效率和降低成本,以及提升机床的自动化和智能化水平的压力不断增大。如何在保障品质的同时加快产出,成为了亟待解决的关键难题。

科尔摩根凭借其在运动控制技术领域的百年经验,针对机床行业的发展需求,推出了由DDL直线电机搭配AKD伺服驱动器构成的解决方案,直击双端面磨床应用痛点。

精准切割
DDL直线电机的直接驱动方式减少了传动误差,提高了定位精度,能达到微米以及纳米级精度。可在低于1秒的循环时间内实现超过1mm的去除余量,工件加工至±0.002mm的平均公差,辅以AKD伺服驱动器采用的高性能快速控制环和高带宽响应,可以将切片送片的匀速阶段速度波动控制在2%以内,在高速裁切控制技术中保证了裁切精度。
强劲推力
负责切片送片的DDL直线电机可达到3152N的峰值推力,从而保证了电机2.5g加速度的出力要求。直线电机能够提供足够的动力以实现高加速度运动,并且在机加工或施加高推力的过程中也能保持刚度,进一步提升了加工效率。
稳定运行
DDL直线电机的设计简化了机械结构,减少了运动部件之间的摩擦和磨损,降低了噪音,延长了使用寿命,并提高了传动效率和系统的可靠性及安全性。AKD伺服驱动器可实现超低速(0.5mm/s)运行,速度波动小,运行平稳。其速度命令、位置命令滤波和延时功能在有效的保证电机刚性的同时,又减小了设备过冲量。大大提高了设备的稳定性,为良品率提供保障。
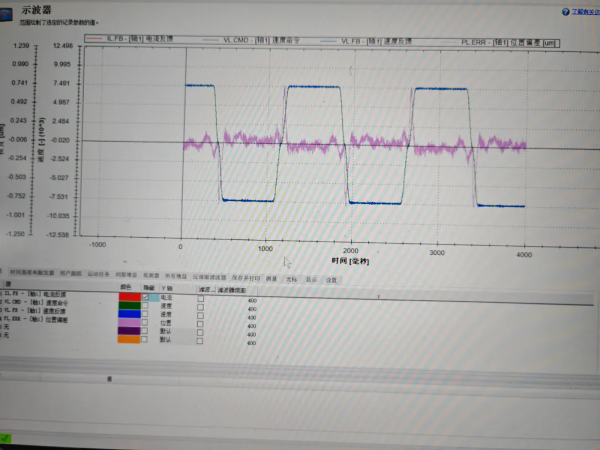
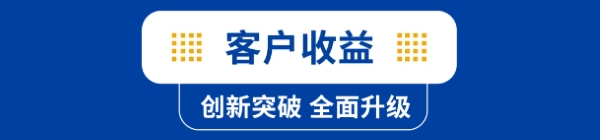
得益于科尔摩根直驱技术解决方案,双端面磨床性能获得了极大的优化升级。65%的定位精度提升及 66%的加速度提升,极大地缩短了加工周期;75%的速度波动控制提升,确保了生产的一致性与稳定性。同时,维护成本因结构简化大幅下降,加之直接驱动方式减少了间接传动的能源损耗,能耗降低了约20%,整体维护成本显著降低。速度和精度的极大改善,使得单位时间内的产量增加了15%,显著提高了生产能力;同时故障率的下降保障了生产的连续性和稳定性。为双端面磨床领域树立了新的标准,展示了批量定制时代的高品质与高效率。
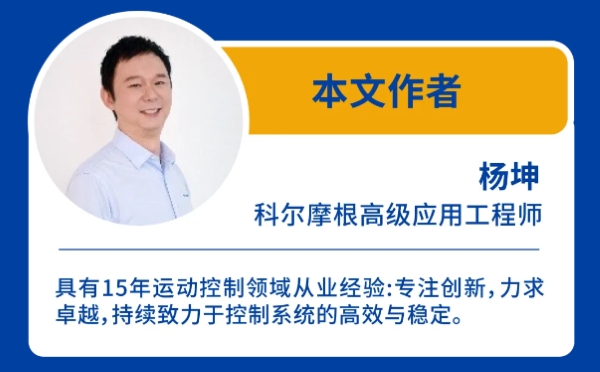